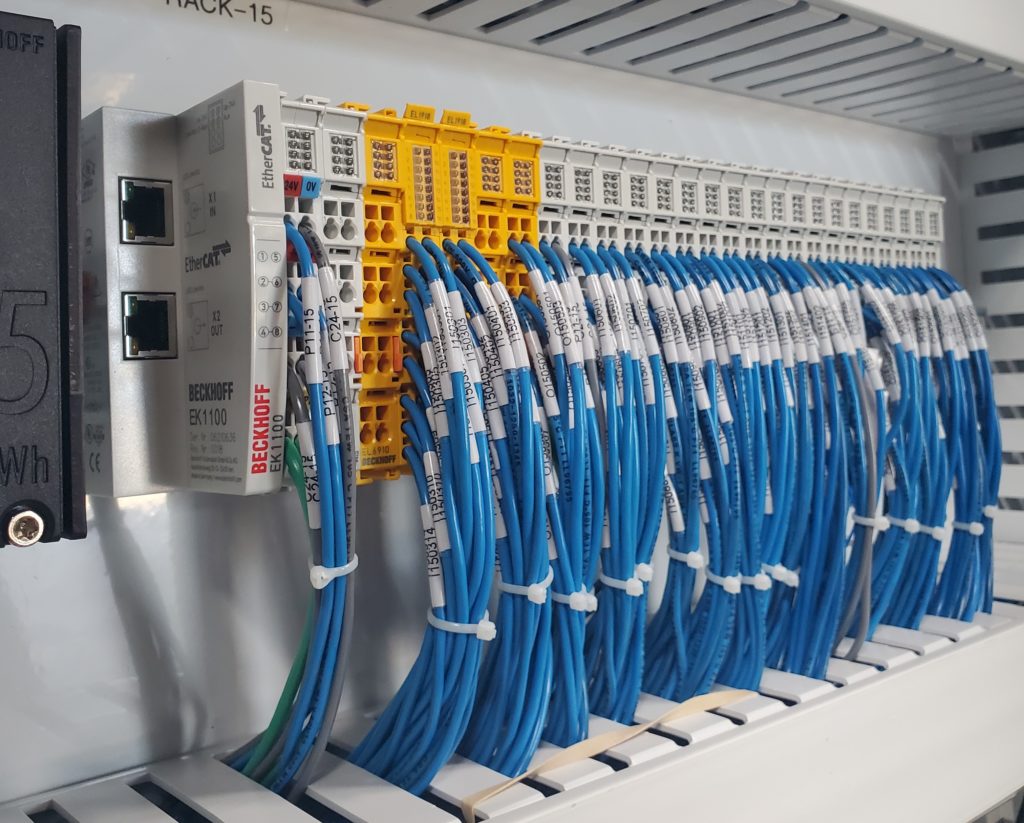
When your brain is functioning slower than normal, your body follows suit. When your brain isn’t firing on all cylinders, it’s nearly impossible to function at a high level.
Think of your PLC system as the brain of your facility.
Your PLC system continuously monitors the state of input devices and makes decisions to control the state of output devices. Your PLC system also gives you the ability to change and replicate the operation or process while collecting and communicating vital information.
So, what should you do when your PLC system becomes obsolete? It’s such an important part of your facility, but knowing when to replace it can be difficult to spot. Then, as with any old hardware and controllers, determining a good time to replace or update your PLC system can be tricky.
Should you wait until your PLC is on its last legs before addressing it? Probably not. Since many components are still backlogged by the manufacturers, buying replacement parts on the internet can be very unreliable.
The decision to migrate to a new system doesn’t have to be a surprise emergency situation, you should be looking for signs of the times well in advance. Here are a few signs to keep an eye on that will give you a good indication of when it’s time to replace your PLC system.
The first thing to check is if your system is using Microsoft Windows 7 or older. Microsoft stopped supporting Windows 7 on January 14, 2020, so if you are still using that software, you haven’t gotten any updates in quite some time now. And running on out-of-date software can really slow down your production.
Since many PLCs are computer-based, using outdated software can hurt you more than simply slowing you down — it can make you vulnerable to cybersecurity issues. If you are still implementing software older than Windows 10, we’d recommend that it’s definitely time to upgrade your user interface, or HMI system, along with your PLC system.
The second thing to consider is, is your installation older than 10 years? Technology has advanced rapidly in the last decade, and if your systems are more than 10 years old, you are missing out on technologies that could significantly increase energy efficiency.
There are newer applications that can save you loads of time in the energy department. For example, the majority of PLC systems now rely on ethernet for communication instead of outdated serial communication. If you’re still using outdated methods and equipment, now may be the time to invest. Today’s cloud-based technologies give you more flexibility for remote access and a clearer, more concise way of communicating across networks.
Third, consider components that are at their end of life, or discontinued. It’s not uncommon that manufacturers will, at times, discontinue certain products that we rely heavily on. Such was the case with Allen Bradley PLC-5.
Many facilities used this technology in their systems and when Allen Bradley began to phase out and eventually discontinue the PLC-5, we were left with two options: 1) Upgrade your system to be compatible with newer technologies, or 2) Continue to use the PLC-5 and hope for the best.
Many discontinued components can only be found in obscure places online. Couple that with the fact that eventually, supplies will run out, it may be time to consider a total system migration. A decision not to upgrade may eventually hinder your ability to expand in the future.
Of course, there are many other reasons that could lead you to upgrade your system. Don’t lose precious time playing catch-up, though, start thinking ahead. Because being proactive about your systems is being proactive about your future. Proper planning now as part of your maintenance strategy will make the migration process easier, make expansion easier, and save you money in the long run!